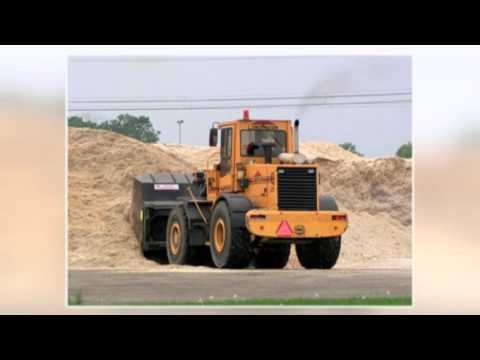
Sisältö
1930-luvun lopulla Yhdysvallat käytti yli puolet maailman luonnonkumin tarjonnasta. Nykyään luonnonkumia löytyy yli 50 000 valmistetusta tuotteesta Yhdysvalloissa, ja Yhdysvallat tuo vuosittain yli 3 miljardia puntaa luonnonkumia. Yli 70 prosenttia nykyaikaisissa valmistusprosesseissa käytetystä kumista on kuitenkin synteettistä kumia.
Luonnonkumin tausta
Luonnonkumi alkaa lateksina. Lateksi koostuu polymeeristä nimeltä polyisopreeni, joka on suspendoitu veteen. Pitkketjuiset molekyylit, jotka koostuvat monista (poly) yksittäisistä yksiköistä (mereistä), jotka on kytketty toisiinsa, muodostavat polymeerejä. Kumi on erityinen polymeerimuoto, jota kutsutaan elastomeeriksi, mikä tarkoittaa, että polymeerimolekyylit venyvät ja taipuvat.
Yli 2500 kasvia tuottaa lateksia, maidon kaltaista mehu-tyyppistä materiaalia. Milkweed saattaa olla tunnetuin lateksia tuottava kasvi monille ihmisille, mutta kaupallinen lateksi on peräisin yhdestä trooppisesta puusta, Hevea brasiliensis. Kuten nimestä voi päätellä, kumipuu on peräisin trooppisesta Etelä-Amerikasta. Yli 3000 vuotta sitten Mesoamerikan sivilisaatiot sekoittivat lateksia aamujuhlomehun kanssa kumin luomiseksi. Lateksin ja aamukilomehden suhteen muuttaminen muutti kumin ominaisuuksia. Hyödyllisistä palloista kumisandaaleihin mesoamerikkalaiset tunsivat ja käyttivät kumia.
Ennen vuotta 1900 suurin osa luonnonkumista tuli luonnonvaraisista puista Brasiliassa. 1900-luvun alkaessa tarjonta ja kysyntä ylittivät tuotannon polkupyörien ja autojen kasvavan suosion myötä. Brasiliasta salakuljetetut siemenet johtivat kumipuuistutuksiin Kaakkois-Aasiassa. 1930-luvulle mennessä luonnonkumin käyttö vaihteli ajoneuvojen ja lentokoneiden renkaista aina 32 kiloon, jotka löytyivät sotilaiden jalkineista, vaatteista ja välineistä. Siihen mennessä suurin osa Yhdysvaltain kumitarpeista tuli Kaakkois-Aasiasta, mutta toinen maailmansota katkoi Yhdysvaltojen suurimman osan tarvikkeistaan.
Luonnonkumin valmistusprosessi
Luonnonkumin valmistusprosessi alkaa lateksin korjuulla kumipuista. Lateksin korjuu kumipuista alkaa pistämällä tai leikkaamalla puun kuoreen. Lateksi valuu kuppiin, joka on kiinnitetty puun leikkauksen pohjaan. Monien puiden lateksimateriaali kertyy suuriin säiliöihin.
Yleisin menetelmä kumin uuttamiseksi lateksista käyttää hyytymistä, prosessia, joka taipuu tai sakeuttaa polyisopreenin massaksi. Tämä prosessi suoritetaan lisäämällä happea, kuten muurahaishappoa lateksiin. Koagulaatioprosessi kestää noin 12 tuntia.
Vesi puristetaan kumin koagulumista ulos rullasarjan avulla. Tuloksena olevat ohuet, noin 1/8 tuuman paksuiset levyt kuivataan savupiippujen puisten telineiden päällä. Kuivausprosessi vaatii yleensä useita päiviä. Tuloksena oleva tummanruskea kumi, jota nykyään kutsutaan rengastuksi savulevyksi, taitetaan paaleiksi toimitettavaksi prosessorille.
Kaikki kumi ei kuitenkaan ole savustettu. Kumia, joka on kuivattu kuumalla ilmalla tupakoinnin sijasta, kutsutaan ilmakuivatuksi levyksi. Tämä prosessi johtaa parempiin kumilaatuihin. Vielä laadukkaampi kumi, nimeltään vaalea kreppikumi, vaatii kaksi hyytymisvaihetta, jota seuraa ilmakuivaus.
Synteettisen kumin luominen
Vuosien mittaan on kehitetty useita erityyppisiä synteettisiä kumeja. Kaikki tulokset johtuvat molekyylien polymeroinnista (yhdistämisestä). Lisäyspolymeroinniksi kutsuttu menetelmä johti molekyylit yhteen pitkiksi ketjuiksi. Toinen menetelmä, nimeltään kondensaatiopolymerointi, eliminoi osan molekyylistä molekyylien ollessa kytkettyinä toisiinsa. Esimerkkejä lisäyspolymeereistä ovat synteettiset kumit, jotka on valmistettu polyklooropreenista (neopreenikumi), öljy- ja bensiininkestävästä kumista, ja styreenibutadieenikumi (SBR), joita käytetään renkaiden pilaantumattomaan kumiin.
Ensimmäinen vakava synteettisen kumin haku aloitettiin Saksassa ensimmäisen maailmansodan aikana. Ison-Britannian saarto estää Saksaa vastaanottamasta luonnonkumia. Saksalaiset kemistit kehittivät polymeerin 3-metyyli-isopreeni (2,3-dimetyyli-1,3-butadieeni) yksiköistä asetonista. Vaikka tämä korvaava metyylikumi oli huonompi kuin luonnonkumi, Saksa valmisti 15 tonnia kuukaudessa ensimmäisen maailmansodan loppuun mennessä.
Jatkuvan tutkimuksen tuloksena saatiin parempaa laatua synteettisiä kumeja. Yleisin tällä hetkellä käytössä oleva synteettisen kumin tyyppi, Buna S (styreenibutadieenikumi tai SBR), kehitti saksalainen yritys I.G. vuonna 1929. Farben. Vuonna 1955 amerikkalainen kemisti Samuel Emmett Horne, Jr. kehitti 98-prosenttisen cis-1,4-polyisopreenin polymeerin, joka käyttäytyy kuin luonnonkumi. Tätä ainetta yhdistettynä SBR: ään on käytetty renkaissa vuodesta 1961.
Kumin käsittely
Kumia, olipa se luonnollinen tai synteettinen, saapuu jalostamoihin (valmistaja) suurissa paaleissa. Kun kumi saapuu tehtaalle, käsittely käy läpi neljä vaihetta: sekoittaminen, sekoittaminen, muotoilu ja vulkanointi. Kumin sekoitusformulaatio ja menetelmä riippuvat kumin valmistusprosessin suunnitellusta tuloksesta.
pahentaa
Yhdistäminen lisää kemikaaleja ja muita lisäaineita kumin mukauttamiseksi käyttötarkoitukseen. Luonnonkumi muuttuu lämpötilan mukana, muuttuessa hauras kylmästä ja tahmea, kova sotku kuumuudesta. Yhdistettäessä lisätyt kemikaalit reagoivat kumin kanssa vulkanointiprosessin aikana kumipolymeerien stabiloimiseksi. Lisälisäaineisiin voi sisältyä lujitteellisia täyteaineita kumin ominaisuuksien parantamiseksi tai vahvistamattomia täyteaineita kumin pidentämiseksi, mikä vähentää kustannuksia. Käytetty täyteaine riippuu lopputuotteesta.
Yleisimmin käytetty lujiteaine on nokea johdettu hiilimusta. Hiilimusta lisää kumien vetolujuutta ja kulumiskestävyyttä. Hiilimusta parantaa myös kumien kestävyyttä ultraviolettihajoamiselle. Useimmat kumituotteet ovat mustia hiilimustan täyteaineen takia.
Kumin suunnitellusta käytöstä riippuen muihin käytettyihin lisäaineisiin voisivat sisältyä vedettömät alumiinisilikaatit lujiteaineena, muut polymeerit, kierrätetty kumi (yleensä alle 10 prosenttia), väsymystä vähentävät yhdisteet, antioksidantit, otsonia kestävät kemikaalit, väriainepigmentit, pehmittimet , pehmentävät öljyt ja homeesta vapautuvat yhdisteet.
Mixing
Lisäaineet on sekoitettava huolellisesti kumiin. Kumin korkea viskositeetti (virtausvastus) vaikeuttaa sekoittamista ilman, että nostetaan kumin lämpötila riittävän korkeaksi (jopa 300 astetta Fahrenheit) aiheuttamaan vulkanointia. Ennenaikaisen vulkanoinnin estämiseksi sekoitus tapahtuu yleensä kahdessa vaiheessa. Ensimmäisessä vaiheessa lisäaineita, kuten hiilimustaa, sekoitetaan kumiin. Tätä seosta kutsutaan master-panokseksi. Kun kumi on jäähtynyt, vulkanointiaineet kemikaalit lisätään ja sekoitetaan kumiin.
muotoiluun
Kumituotteiden muotoilu tapahtuu neljällä yleisellä tekniikalla: suulakepuristus, kalanterointi, pinnoitus tai muovaus ja valu. Useita muotoilumenetelmiä voidaan käyttää lopputuotteesta riippuen.
Suulakepuristus koostuu erittäin muovisen kumin pakottamisesta ruuvipuristimen sarjan läpi. Kalanterointi vie kumin sarjan yhä pienemmiksi rullien välisiksi rakoiksi. Rullamuottimen prosessissa yhdistyvät suulakepuristus ja kalanterointi, jolloin saadaan parempi tuote kuin kummassakin yksittäisessä prosessissa.
Pinnoitteella kalanterointiprosessilla levitetään kumikerros tai kumi pakotetaan kankaaseen tai muuhun materiaaliin. Renkaat, vedenpitävät kangas teltat ja sadetakit, kuljetinhihnat sekä puhallettavat lautat valmistetaan päällystämällä materiaaleja kumilla.
Kumituotteet, kuten kenkäpohjat ja korkokengät, tiivisteet, tiivisteet, imukupit ja pullonpysäyttimet valettiin muotilla. Muotoilu on myös askel renkaiden valmistuksessa. Kolme ensisijaista kumin muovausmenetelmää ovat puristusmuovaus (käytetään renkaiden valmistukseen muiden tuotteiden joukossa), siirtomuovaus ja ruiskuvalu. Kumin vulkanointi tapahtuu muovausprosessin aikana eikä erillisenä vaiheena.
vulkanointi
Vulkanointi saattaa loppuun kumin valmistusprosessin. Vulkanointi luo ristisidokset kumipolymeerien välillä, ja prosessi vaihtelee riippuen lopullisen kumituotteen vaatimuksista. Vähemmän ristisidoksia kumipolymeerien välillä luo pehmeämpi, taipuisampi kumi. Ristisidosten lukumäärän lisääminen vähentää kumin joustavuutta, jolloin kumia kovenee. Ilman vulkanointia kumi pysyisi tahmeana kuumana ja haurasta kylmänä, ja se mädäntyisi paljon nopeammin.
Vulkanointi, jonka Charles Goodyear löysi alun perin vuonna 1839, vaati rikin lisäämistä kumiin ja seoksen kuumentamisen 280 ° F: seen noin viiden tunnin ajan. Nykyaikaisessa vulkanoinnissa käytetään yleensä pienempiä määriä rikkiä yhdistettynä muihin kemikaaleihin vähentääksesi kuumennusajan 15 - 20 minuuttiin. On kehitetty vaihtoehtoisia vulkanointitekniikoita, joissa ei käytetä rikkiä.